views
Shell and tube warmth exchangers are a number of the maximum widely used sorts of heat exchangers in industrial techniques, regarded for his or her durability, adaptability, and efficiency in moving warmness among fluids. In this system, one fluid flows via a package of tubes while every other flows over the tubes inside a sealed shell, taking into account thermal electricity alternate without mixing. The dependable design and scalable capacity of shell and tube heat exchangers have made them a desired desire for lots tactics, specifically the ones overseen by using any skilled Industrial products producer.
Core Components and Functional Design
The Shell
The shell is a cylindrical container that homes the tube package. It enables the drift of one of the working fluids, usually the one with the higher volume or extra fouling capability. The shell layout can range in diameter and period relying at the precise heat responsibility and glide characteristics required for the application.
The Tube Bundle
Inside the shell, a fixed of parallel tubes paperwork the center of the warmth change process. These tubes are frequently made of metal alloys decided on for his or her thermal conductivity and corrosion resistance. Fluids in the tubes change warmth with the fluid circulating thru the shell, with the 2 flows ultimate bodily separated.
Tube Sheets and Baffles
The tube sheets are plates that hold the tubes in region at every give up of the bundle. Baffles are strategically positioned inside the shell to direct the waft of shell-facet fluid across the tubes more than one times, increasing turbulence and enhancing heat switch performance. These baffles additionally serve to assist the tubes and limit vibration.
How Heat Transfer Occurs
Crossflow and Counterflow Mechanisms
Heat is transferred through the tube walls by way of conduction and is more advantageous by way of the turbulence created by using baffles. In a counterflow configuration, the fluid inside the shell flows in the opposite route of the fluid in the tubes, which maximizes the temperature gradient and therefore the thermal switch charge. Crossflow designs are also used, depending on the system’s thermal wishes.
Influence of Flow Rates
The price of fluid drift on both the shell and tube facets extensively impacts the warmth exchanger’s efficiency. Higher flow rates usually enhance heat transfer however can also cause improved stress drop and higher operational charges. Striking a balance is key in optimizing performance.
Materials Used in Construction
Metal Alloys
Common materials encompass carbon metallic, stainless-steel, copper alloys, and titanium. The choice relies upon on the corrosiveness of the fluids, temperature extremes, and strain conditions. Stainless metallic is frequently used for its corrosion resistance and strength.
Protective Linings and Coatings
In corrosive environments, internal linings or outside coatings may be implemented to extend the exchanger’s lifespan. This is specially important in chemical or seawater applications wherein aggressive fluids are concerned.
Types of Shell and Tube Heat Exchangers
Fixed Tube Sheet Design
This is the most effective and most value-effective layout. The tube bundle is completely constant to the shell, which makes it appropriate for easy fluids. However, it limits the capacity to look at or easy the interior of the tubes, which can be a disadvantage in dirty provider packages.
U-Tube Design
In this configuration, the tubes are bent right into a U-shape and glued at most effective one cease. This lets in for differential thermal growth among the shell and the tubes. It also makes it simpler to remove the tube package deal for cleaning, even though person tube cleaning may be extra complex.
Floating Head Design
This type permits one quit of the tube package deal to transport freely within the shell, accommodating thermal enlargement and simplifying upkeep. It is right for offerings wherein fouling is probable, because the entire package can be eliminated for inspection and cleansing.
Industrial Applications of Shell and Tube Heat Exchangers
Power Generation
In power flora, shell and tube exchangers are utilized in condensers to cool steam again into water after it passes through generators. They are also utilized in feedwater heaters and auxiliary cooling systems.
Oil and Gas Industry
These exchangers handle excessive pressures and corrosive fluids, making them appropriate for refining procedures, gas treatment, and petrochemical operations. Their sturdy creation allows them to resist harsh working conditions.
HVAC and Refrigeration
Shell and tube designs are used in large-scale heating and cooling systems for temperature regulation. They function evaporators and condensers in chillers and provide dependable thermal alternate for building climate manage.
Chemical Processing
In chemical flora, shell and tube exchangers help control manner temperatures, facilitate reaction situations, and condense chemical vapors. Their modular layout lets in integration into complex process structures.
Benefits of Using Shell and Tube Heat Exchangers
High Thermal Efficiency
The huge surface place supplied via the tube bundle permits for effective warmness transfer even in compact designs. The inclusion of baffles will increase turbulence, further enhancing thermal efficiency.
Pressure and Temperature Resilience
Shell and tube exchangers can take care of excessive pressures and temperature differentials, that is why they're used in important and worrying business settings. Their design permits for personalisation to healthy specific stress ratings and thermal loads.
Maintenance and Cleaning Options
With various layout alternatives to be had, those exchangers can be tailored for ease of protection. Floating head and U-tube models offer the capability to easy the tube package very well, which is critical in strategies where fouling is common.
Challenges and Limitations
Fouling and Scaling
Over time, scale, sediment, or biological increase can accumulate on the warmth switch surfaces. This fouling reduces efficiency and can boom maintenance frequency. Appropriate material choice and periodic cleaning are vital.
Pressure Drop
Increased fluid speed and baffle layout can purpose better stress drops, which might also affect system performance. Careful engineering and computational modeling are essential to optimize the stability between warmth transfer and stress loss.
Size and Weight
These exchangers can be huge and heavy, mainly in high-capacity systems. Installation and assist systems have to be designed for this reason, that could add to the capital value of the device.
Innovations and Design Advancements
Enhanced Tube Surfaces
Modern production strategies have brought about the development of tubes with more advantageous internal or external surfaces to improve turbulence and boom heat switch rates. These improvements help reduce the overall length of the exchanger.
Computational Fluid Dynamics (CFD)
Engineers use CFD to simulate fluid float and warmth switch within the exchanger. This facilitates in designing greater efficient and compact units, specifically for custom or high-overall performance programs.
Modular Skid-Mounted Units
Skid-installed heat exchanger structures come pre-assembled and pre-examined. These reduce installation time and allow for higher best manipulate. They are particularly beneficial in offshore and remote installations.
Maintenance and Operational Best Practices
Regular Inspection
Visual and ultrasonic inspections can detect wear, corrosion, or fouling before they impact performance. Scheduled maintenance ensures lengthy-time period reliability.
Cleaning Methods
Chemical cleaning, hydro-jetting, and mechanical brushing are usually used methods relying on the sort and volume of fouling. Proper cleansing extends the operational lifestyles of the system.
Monitoring and Instrumentation
Pressure and temperature sensors can help discover overall performance drops early. Automated manipulate systems can regulate waft quotes or provoke alarms based on operating parameters.
Conclusion
Shell and tube warmness exchangers continue to serve as a backbone technology throughout numerous industrial sectors due to their sturdy layout, performance, and flexibility. From electricity generation and petrochemicals to HVAC and water treatment, those structures take care of complicated thermal challenges with precision. Supported by way of the know-how of an industrial products manufacturer, the right shell and tube configuration can supply long-lasting value, optimized overall performance, and compliance with evolving operational needs.
With ongoing innovations in materials, simulation equipment, and production techniques, shell and tube heat exchangers are evolving to satisfy the contemporary needs of sustainability, reliability, and manner efficiency.
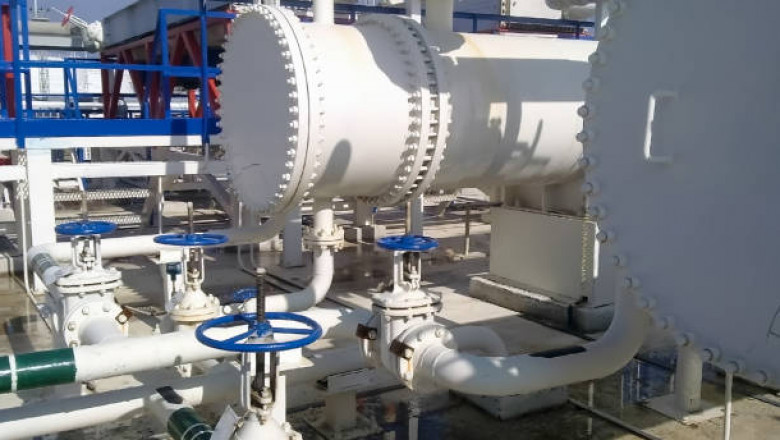

Comments
0 comment