views
This cutting-edge technology is rapidly gaining popularity in sectors such as automotive, aerospace, shipbuilding, power generation, and manufacturing. But what exactly makes an industrial laser cleaner stand out in such demanding environments? Let's explore how this tool is reshaping the future of industrial cleaning, where speed, accuracy, and eco-friendliness are critical.
How Does an Industrial Laser Cleaner Work?
At its core, an industrial laser cleaner utilizes a highly focused laser beam to remove unwanted substances from metal surfaces. The process, known as laser ablation, involves directing laser energy at the contaminant. This energy heats the material to the point where it either vaporizes or is ejected from the surface due to the intense light pulses.
Unlike traditional methods that physically grind or scrape a surface, laser cleaning works without contact. This non-invasive approach not only preserves the integrity of the base material but also allows for highly controlled and repeatable results.
Laser cleaners can be configured with varying power levels, pulse durations, and beam sizes depending on the specific cleaning task. From removing light oxidation on aluminum to stripping thick rust layers from steel, the technology is remarkably versatile.
Industrial Applications of Laser Cleaning
The industrial laser cleaner has found its place across various sectors due to its flexibility and reliability. Here are some areas where it's making a significant impact:
1. Rust Removal in Manufacturing Plants
Rust not only affects aesthetics but also weakens structural integrity. Laser cleaners provide an efficient way to remove rust without damaging the substrate. This is especially valuable in preparing surfaces for welding or painting, ensuring a clean bond or coat.
2. Paint Stripping in Aerospace and Automotive
Airplanes and automobiles often require repainting, which involves stripping existing layers of paint. Traditional chemical stripping methods can be hazardous and time-consuming. Industrial laser cleaners provide a safer, faster alternative, especially for delicate aerospace materials like titanium or carbon composites.
3. Weld Preparation and Post-Weld Cleaning
Before welding, surfaces need to be free from oils, oxides, and contaminants. Post-weld cleaning involves removing slag and discoloration. Laser cleaners can handle both tasks with ease, improving welding quality and reducing the need for rework.
4. Mold Cleaning in Manufacturing
Mold tools used in plastic or rubber manufacturing often accumulate residues that affect product quality. Manual cleaning can damage the mold's fine details, but laser cleaning offers a precise, damage-free solution, prolonging the tool's life.
5. Cultural Heritage and Restoration Work
Even outside traditional industries, laser cleaners have a role. In restoration projects, where preserving the original material is essential, these devices offer the gentlest cleaning method available—removing grime, soot, or corrosion from historic artifacts and monuments.
Safety Considerations and Operator Training
While the industrial laser cleaner is designed to be safe when used properly, it's essential that operators receive proper training. Direct exposure to laser beams can be hazardous, so protective equipment like safety goggles, shields, and controlled environments are crucial. Modern systems are often equipped with safety interlocks and automatic shut-off mechanisms to prevent accidents.
Training programs often include understanding the beam characteristics, setting up the cleaning parameters, handling the fiber optics, and basic troubleshooting. With appropriate safety protocols in place, the technology can be used safely and effectively even in high-throughput environments.
Environmental Impact and Sustainability
One of the standout aspects of industrial laser cleaners is their eco-friendliness. Traditional cleaning often involves consumables like chemicals, water, or abrasives that generate waste and pose disposal issues. Laser cleaning, on the other hand, eliminates the need for these materials. There’s no chemical runoff, no airborne abrasive dust, and no wastewater.
In fact, many companies are turning to this technology not just for efficiency, but also to meet growing environmental regulations and to reduce their carbon footprint. It's a cleaner solution in every sense of the word—both literally and figuratively.
Industrial Laser Cleaner vs. Traditional Methods
While we won’t delve into a traditional advantages-disadvantages list, it's important to recognize that the industrial laser cleaner represents a paradigm shift. Instead of adding complexity to the workflow, it simplifies it. There’s no need for secondary cleanup, material disposal, or post-treatment in many cases. The process integrates seamlessly into existing production lines, even allowing for automation and robotic integration.
Moreover, the repeatability and precision make it ideal for industries where consistency and quality are paramount. Whether you're cleaning 10 parts or 10,000, the results remain the same.
Factors to Consider Before Investing
Choosing the right industrial laser cleaner involves understanding your specific cleaning needs. Factors like material type, contaminant thickness, area coverage, and required throughput all influence the choice of equipment.
Some systems are designed for portability—handheld laser cleaners that technicians can easily move around a facility. Others are large, automated systems integrated into production lines. The laser power (ranging from 50W to over 1000W), beam quality, and pulse frequency also vary widely across models.
You’ll also want to consider maintenance requirements, customer support, software control options, and the ease of switching between different cleaning modes. Reputable suppliers typically offer on-site demonstrations or trials, allowing businesses to evaluate the performance firsthand.
Why Demand Is Growing Worldwide
Global industries are in a constant race to optimize processes, reduce downtime, and improve sustainability. The industrial laser cleaner hits all these targets. As the cost of laser technology decreases and awareness grows, more companies are realizing the long-term value it offers.
It’s not just about cleaning—it’s about redefining how industries approach surface preparation. Countries with stringent environmental regulations are especially seeing a spike in adoption, and even smaller manufacturers are investing in compact models.
Additionally, with the rise of Industry 4.0, smart factories are looking for tools that offer digital integration, minimal manual intervention, and high precision. Laser cleaners, particularly those with software interfaces, data logging, and remote monitoring capabilities, are perfectly aligned with this trend.
Final Thoughts
The industrial laser cleaner is more than just a tool—it’s a transformation in how industries approach surface maintenance and cleanliness. By offering a precise, non-contact, and environmentally conscious solution, it bridges the gap between traditional labor-intensive methods and the demands of modern manufacturing.
Whether you're running a factory, managing a restoration project, or seeking a safer, more effective cleaning solution, the industrial laser cleaner is worth your attention. As the technology continues to evolve, it's likely to become a staple in every serious industrial toolkit.
Want to experience it for yourself? Explore trusted suppliers and see how laser cleaning can elevate your operations with precision and power.
Would you like a custom promotional message or ad copy to go along with this article?
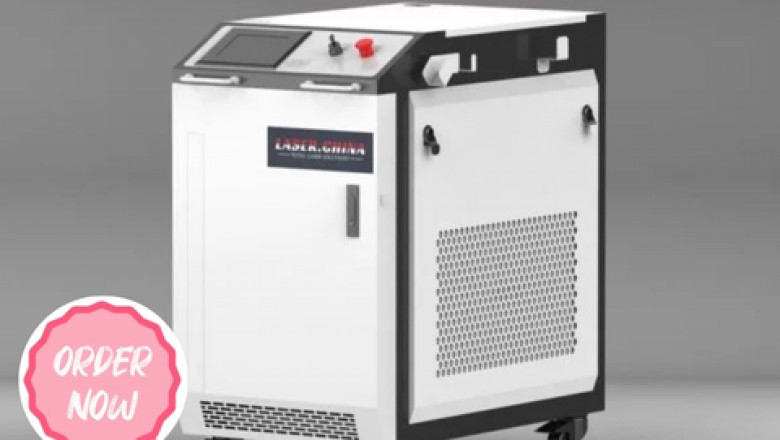

Comments
0 comment