views
The Role of Industrial Water Chillers and Pass Boxes in Modern Industries
Temperature control remains inevitable for achieving quality, consistency, and efficiency in various industrial processes. An industrial water chiller is defined as a cooling system installed to remove excessive heat from equipment, processes, and places in a manufacturing facility, laboratory, data center, and the like. Industrial chillers do not compare with air conditioners since they operate continuously for high capacity and tough-duty operations. Chilled water is pumped through a heat exchanger where the process heat is absorbed and expelled using refrigeration cycles. Thus enabling any heat-sensitive machinery, such as plastic molding systems, CNC machines, printing equipment, or even food processing lines, to operate under safe load conditions without any overheating.
Industrial water chillers do not only help in cooling but also improve the product quality and the lifetime during which it operates. High heat may deform the product, damage machinery, or interrupt production cycles. Chillers keep the right process temperature, so downtime, hazards, and more energy money spent are avoided. Today, chillers come with digital controls, variable speed compressors, and environment-friendly refrigerants to meet both accuracy as well as sustainability.
Key Features and Applications of Industrial Water Chillers
The functions of industrial water chillers speak to their versatility and efficiency. In the plastics sector, chillers are used to cool injection molds and extruders with rapid cycle times and surface finish enhancement. In the food and beverage industry, the chillers help regulate temperatures in fermentation areas, storage of dairy products, and sanitation related to meat processing plants. They are also used to chill reactors, packaging machinery, and environmental control in pharmaceutical manufacturing. Chillers play a major part in this industry to run the central cooling systems of commercial buildings and data centers.
Industrial chillers are differentiated from other chillers by means of custom configurations and stringent performance specifications. They come in air-cooled and water-cooled units, whichever is best for the operating conditions and space available. Higher-end models use smart diagnostics and offer remote monitoring and fault detection. With these diagnostics, maintenance teams can now monitor performance in real time, detect inefficiencies early, and avert catastrophic breakdowns. Modernisation over IoT and energy management systems has made the chillers efficient, traceable, and maintainable, with maintainability being the key priority for industries with lean operations and sustainable development.
Protection against Product Contamination and Process Variation by Pass Box in Cleanrooms
In cleanroom environments, where maintaining cleanliness and controlling contamination are crucial, a pass box clean room is essential for maintaining air purity. The pass-box cleanroom system is a sealed enclosure for environmental hazard exclusion, used to transfer materials between clean and unclean environments without disturbing the sterile environment. By preventing human entry and cross-contamination, pass box clean rooms safeguard the product and the process. They are generally mounted on the cleanroom's walls and comprise interlocking doors, eliminating simultaneous opening from either side.
Static pass boxes are favourable for the transfer of nonliving material, like tools, samples, or documents. Dynamic pass boxes use HEPA filters with blower systems, allowing a stream of air to pass through the box before the internal door is opened, which effectively keeps items free of particulates. Syntec Airflow Systems and other reputable manufacturers offer custom-built pass boxes with features such as UV lights and electromagnetic interlocks, as well as stainless-steel interiors, to meet standards that are industry-specific.
Cleanroom Integration: Where Industrial Cooling Meets Air Purity
Today's manufacturing and R&D facilities often find industrial water chillers and pass boxes for clean rooms side by side, but they serve different purposes. While chillers maintain the thermal environment necessary for precision equipment or temperature-sensitive materials, pass boxes ensure that during transfer operations, these environments are kept free from contamination. By relating these systems to the HVAC and cleanroom systems of the facility, operational efficiency and compliance with regulatory standards such as GMP, ISO 14644, and FDA are enhanced.
In industries including pharmaceuticals, electronics, and aerospace, temperature glitches or airborne particulates entering the production area can cause product failures or regulatory breaches. Thus, the facility design is for interlinked environmental control systems, where cleanrooms will require chillers for air conditioning and cooling of equipment, whereas pass box clean rooms are needed to facilitate controlled movement of materials. This integrated approach ensures that each aspect of the production process-from temperature regulation to handling of materials strictly controlled and optimised for top-quality, consistency, and safety.
Bottom Line:
As industries develop ever greater technologies and regulatory standards become tighter and tighter, investment in high-performance systems such as industrial water chillers and pass box clean rooms has become not only a necessity but a strategy. They help make sure that operations run smoothly and products meet quality expectations while keeping every environment safe for the welfare of the people and processes. With more available solutions being automated, energy-efficient, and customisable, companies can now adapt their environmental control requirements to their very needs, without compromising on sustainability or performance.
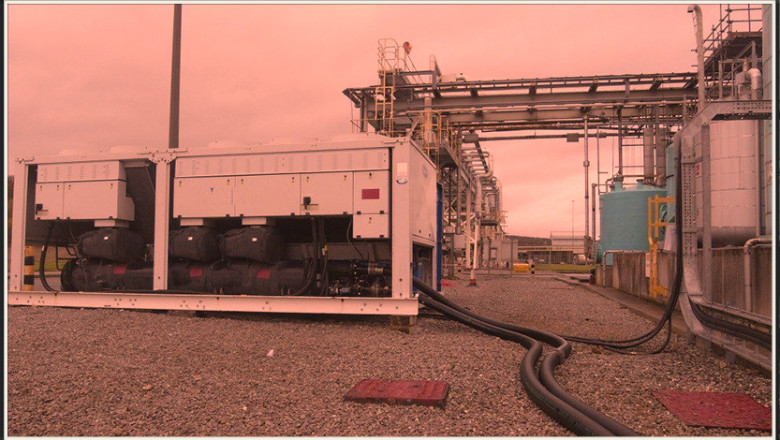

Comments
0 comment