views
Let’s dive deep into how laser beam welding works, why it matters in modern manufacturing, and what makes it a powerful investment for industries looking to enhance their output and product quality.
What is a Laser Beam Welding Machine?
A laser beam welding machine uses a concentrated beam of light—yes, light—to melt and fuse materials together, typically metals. Unlike gas or arc welding, which involves heating materials with a flame or electric current, laser welding focuses high-intensity photons onto a specific spot. This focus enables localized heating, resulting in an exceptionally narrow weld zone.
The core components of a laser beam welding machine include:
-
A high-powered laser source (such as fiber, CO₂, or Nd:YAG)
-
Optical focusing systems
-
Beam delivery tools (such as mirrors or fiber optics)
-
Automated or manual control systems
Once configured, the laser beam travels through the optics and lands on the metal surface, instantly raising its temperature to the melting point. As the beam moves along the joint, it leaves behind a solidified weld—precise, minimal in distortion, and incredibly strong.
The Science Behind the Strength
The strength of a weld depends on several physical and metallurgical factors, and this is where the laser beam welding machine excels.
-
High Energy Density:
The laser beam concentrates a large amount of energy into a very small area. This leads to a fast melt rate and a narrow weld. Since the surrounding material remains largely unaffected, the heat-affected zone (HAZ) is minimized, preserving the metal’s original properties. -
Full Penetration Welding:
A common challenge with conventional welding is achieving full penetration without causing surface defects. With laser welding, even thick metals can be fused entirely through their depth, thanks to the keyhole effect. This keyhole is a vapor cavity that allows deep penetration with minimal surface disturbance. -
Controlled Metallurgy:
Since the process is so fast and localized, there's less time for undesirable microstructures (like large grain growth or porosity) to develop. This results in a homogeneous, defect-free weld with high mechanical integrity. -
No Filler Material Required:
In many cases, a laser beam welding machine doesn’t need additional filler metals. This makes the joint purer and eliminates potential weaknesses introduced by mismatched filler materials. -
Repeatable Quality:
Consistency is crucial in sectors like aerospace, automotive, and electronics. Laser welding’s precision is maintained from one weld to the next, ensuring uniformity across production lines.
Applications Across Industries
The laser beam welding machine is not a one-size-fits-all tool, but its versatility has made it indispensable across several key sectors.
Automotive Industry
Car manufacturers rely heavily on laser welding for body structures, battery components in EVs, and engine parts. The speed and accuracy of this method allow them to produce lighter vehicles with stronger joints, essential for both safety and efficiency.
Aerospace and Aviation
Airplanes demand extremely durable joints without compromising on weight. Laser welding delivers high-strength joints on titanium and aluminum alloys—both widely used in aircraft construction.
Medical Devices
Implants and surgical tools require incredibly clean and precise welds, with no room for contamination. Laser beam welding is ideal for stainless steel, titanium, and cobalt-chromium alloys in this industry.
Electronics and Micro-Welding
When working with tiny parts, such as battery terminals or sensor housings, laser welding allows manufacturers to avoid damaging sensitive components. It creates secure connections with minimal thermal load.
Tool and Die Manufacturing
Repairing or creating molds and dies demands fine control. Laser welding machines offer the precision needed to restore or build components without warping or compromising the mold shape.
The Evolution of Laser Beam Welding Machines
Over the years, laser welding machines have undergone significant transformation. Early models were bulky and limited in scope. Today’s machines are compact, computer-controlled, and integrate with robotic arms for maximum flexibility.
Modern machines use:
-
Fiber lasers for energy efficiency and long service life
-
Automated scanning systems to increase weld speeds
-
Integrated cooling systems to handle long hours of operation
-
Smart sensors that provide real-time feedback on weld quality
As technology continues to advance, the capabilities of laser beam welding machines only grow—making them more accessible and powerful.
Cost Efficiency and Productivity Gains
Though a laser beam welding machine may seem like a heavy investment initially, the long-term savings are significant. Here's why:
-
Reduced Rework: Clean, defect-free welds mean fewer repairs and waste.
-
Lower Material Usage: No filler material and minimal post-processing save money.
-
Faster Production: Higher weld speeds improve throughput, even on complex geometries.
-
Longer Equipment Lifespan: Fiber lasers, for instance, can run for tens of thousands of hours with minimal maintenance.
For mass production environments, these savings quickly outweigh the upfront equipment cost, making the laser beam welding machine a smart investment.
Installation and Setup Considerations
Before integrating a laser beam welding machine into your workflow, some critical factors must be evaluated:
-
Material Compatibility: While most metals can be laser welded, each behaves differently. You’ll need to calibrate your machine for the specific metal type, thickness, and joint design.
-
Joint Preparation: Clean, well-aligned joints are essential. Any debris or gap can disrupt the laser’s effect.
-
Safety Measures: Laser machines are extremely powerful and require protective shielding, operator training, and laser-safe environments to ensure workplace safety.
-
Ventilation and Extraction: The high temperatures can release fumes, especially when working with coated or treated metals. Fume extraction systems are vital for worker health.
Integration with Automation
Laser beam welding machines pair well with automation systems. In fact, many industrial robots are designed to carry laser heads or work alongside laser stations. These integrated systems allow for:
-
24/7 operation
-
Increased precision with robotic motion control
-
Reduced human error
-
Easy repeatability for large production batches
Whether you’re building car frames or smartphone components, automation ensures that every weld meets your quality standards.
Why Businesses Are Making the Shift
As competition intensifies across all manufacturing sectors, businesses are constantly seeking tools that offer both quality and efficiency. The laser beam welding machine answers this demand with unmatched performance.
Companies switching from conventional welding methods to laser systems report:
-
Stronger product lifespans
-
Fewer customer complaints about weld failures
-
Shorter production cycles
-
Better overall product aesthetics
In customer-facing products, a clean weld not only performs better—it looks better too. This visual appeal often translates into higher perceived value.
Final Thoughts
The laser beam welding machine is not just another piece of industrial equipment—it’s a transformative tool for modern manufacturing. Its ability to create strong, precise, and clean welds on a variety of materials makes it an essential part of industries aiming for high standards and efficient operations.
If you’re considering upgrading your production line, exploring new fabrication methods, or simply looking to future-proof your manufacturing processes, investing in a laser beam welding machine is a strategic step forward. Its applications span across industries, and its performance speaks for itself in every weld.
This is not just about better welding; it’s about stronger products, faster production, and smarter business.
Would you like help selecting a specific laser beam welding machine model for your industry?
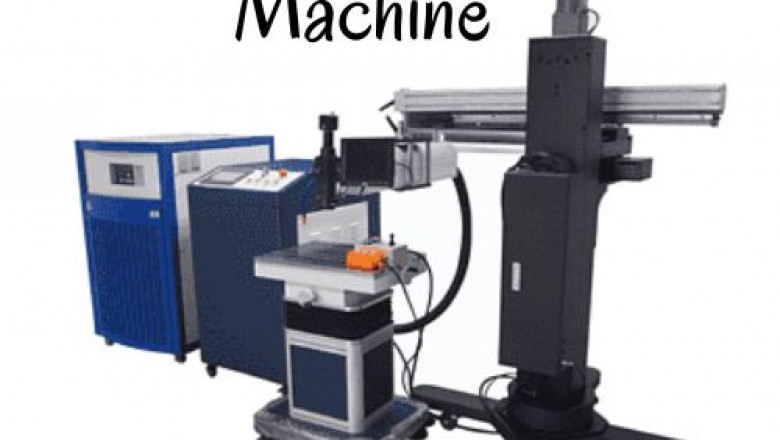

Comments
0 comment